Pistachio Nuts
Well-known member
Carpenters, am in need of a solution! ?
We have two long tables (126" in length) that we want to be able to dismantle and put back together for easier transport. The thing is, there's no visible screws, and all the joints have been glued together. The table itself is made of particle board with a laminated top and sides.
Is it possible to dismantle this thing and install joints that can be easily taken apart (and put back together again)? If so, is this even worth doing?
Thanks for any help, dudes!
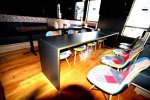
We have two long tables (126" in length) that we want to be able to dismantle and put back together for easier transport. The thing is, there's no visible screws, and all the joints have been glued together. The table itself is made of particle board with a laminated top and sides.
Is it possible to dismantle this thing and install joints that can be easily taken apart (and put back together again)? If so, is this even worth doing?
Thanks for any help, dudes!

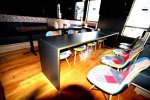
Last edited: