Priller
Well-known member
So having bought an old RC51 for trackday fun, I inevitably started looking at the threads on RC51 forums for 'cheap' upgrades. One that came up was swapping the '00-01 swingarm (SP-1) for the longer and lighter '02-05 (SP-2) unit. I found one in decent nick for a good price, and figured, 'how hard can this be?' Famous last words...
After figuring out the specialty tools, I popped off the nut (part 17 on the fiche below). First warning, as it had a fair bit of corrosion and took a good pull to break free. After that, I loosened the adjuster nuts (parts 18, look like castle nuts) and went to spin out the pivot bolt itself (part 7). The bolt did eventually come free, but it took a 24" breaker bar with an extension to get it shifted. I spun it out slowly, spinning it back in periodically to help clear as much of the corrosion as possible. It took force all the way out, and never came fully free. Towards the end of the threading, it started taking the swingarm with it, so that as I turned the bolt, I'd have to pull the swingarm back down to carry on. It also got much harder to turn at this point. I should also mention that I had hammered on the opposite end of the bolt at various points, and used liberal amounts of Liquid Wrench, neither of which seemed to make any difference.
The problem I have now is that the threading on the adjustment nut (part 9) is out of the frame, and the swingarm bolt just spins, but it just won't come free. I've tried whacking it with a 2 1/2" lb mini sledge, and put an air chisel into a socket adaptor to try to rattle it free, but no luck.
The bolt should just come free once the nut is off, as it's not actually threaded into anything, but it's stuck solid. It's spinning (with resistance) and the swingarm itself moves freely. This leads me to think I have threaded the sleeve (part 29 in the second fiche) out of the crankcase (and possibly crushed some bearings in the process, hence the rotating swingarm) but that the two are fused together.
The next obvious step is to get a much bigger hammer and just add brute force to try and pop the bugger free by whacking on the opposite end (right side). I'm not fussed about any of the parts except for the frame and crankcase, as I have different ones for the replacement swingarm. My main concern is possibly damaging the frame, though, and I was wondering if anyone had a more subtle solution? I'm quite concerned that I've already stripped the outside few threads when the adjuster nut (part 9) spun as it got to the end of the frame. The bike is also up on jack stands, so I'll have to figure out additional support before I really start to go to town.
One other note: I've also supported the engine, just in case the case isn't aligned and is binding. This had made no difference...
Here's a pic of the bolt end (parts 7 & 9 - not my bike, but it looks similar, bar the rusty rearset bolt):
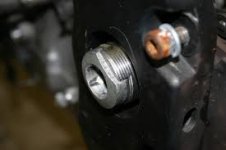
And a fiche for the swingarm:
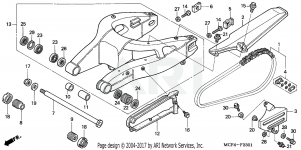
A fiche for the case:
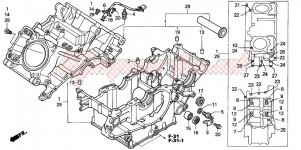
And a pic of the steel sleeve in a removed case:
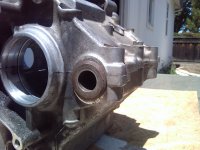
After figuring out the specialty tools, I popped off the nut (part 17 on the fiche below). First warning, as it had a fair bit of corrosion and took a good pull to break free. After that, I loosened the adjuster nuts (parts 18, look like castle nuts) and went to spin out the pivot bolt itself (part 7). The bolt did eventually come free, but it took a 24" breaker bar with an extension to get it shifted. I spun it out slowly, spinning it back in periodically to help clear as much of the corrosion as possible. It took force all the way out, and never came fully free. Towards the end of the threading, it started taking the swingarm with it, so that as I turned the bolt, I'd have to pull the swingarm back down to carry on. It also got much harder to turn at this point. I should also mention that I had hammered on the opposite end of the bolt at various points, and used liberal amounts of Liquid Wrench, neither of which seemed to make any difference.
The problem I have now is that the threading on the adjustment nut (part 9) is out of the frame, and the swingarm bolt just spins, but it just won't come free. I've tried whacking it with a 2 1/2" lb mini sledge, and put an air chisel into a socket adaptor to try to rattle it free, but no luck.
The bolt should just come free once the nut is off, as it's not actually threaded into anything, but it's stuck solid. It's spinning (with resistance) and the swingarm itself moves freely. This leads me to think I have threaded the sleeve (part 29 in the second fiche) out of the crankcase (and possibly crushed some bearings in the process, hence the rotating swingarm) but that the two are fused together.
The next obvious step is to get a much bigger hammer and just add brute force to try and pop the bugger free by whacking on the opposite end (right side). I'm not fussed about any of the parts except for the frame and crankcase, as I have different ones for the replacement swingarm. My main concern is possibly damaging the frame, though, and I was wondering if anyone had a more subtle solution? I'm quite concerned that I've already stripped the outside few threads when the adjuster nut (part 9) spun as it got to the end of the frame. The bike is also up on jack stands, so I'll have to figure out additional support before I really start to go to town.
One other note: I've also supported the engine, just in case the case isn't aligned and is binding. This had made no difference...
Here's a pic of the bolt end (parts 7 & 9 - not my bike, but it looks similar, bar the rusty rearset bolt):
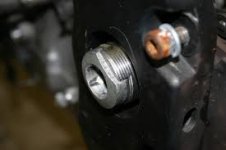
And a fiche for the swingarm:
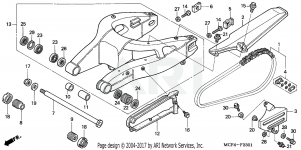
A fiche for the case:
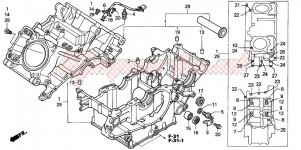
And a pic of the steel sleeve in a removed case:
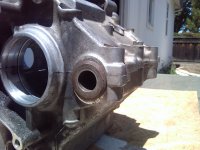